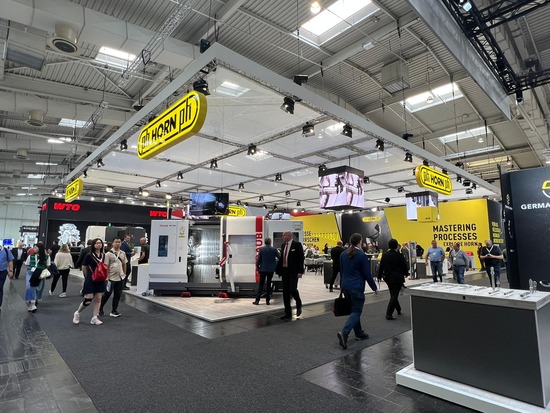
P Horn Pushes Boundaries At EMO Hannover 2023
P Horn has a legacy of excellence and innovation in the manufacturing industry, consistently pushing the boundaries of what’s possible, as demonstrated in EMO Hannover 2023.
The world-renowned cutting tools players unveiled its latest at the show, maintaining its commitment to quality and standards in one of the world’s leading metalworking shows.
New High-Performance Grade For Thread Whirling
SG3P is the name of the newly developed Horn high-performance grade offering the user new possibilities in terms of performance and tool life when whirling medical screws. The new carbide grade also enables shorter cycle times for thread production thanks to higher cutting values, including when processing materials that are difficult to machine.
In addition, the combination of an ultra-fine grain carbide powder and the high temperature resistant coating results in high process reliability and better component quality. The carbide grade is available for all standard Horn thread whirling systems. Furthermore, in-house coating enables fast delivery times.
The production of bone screws must necessarily be carried out using a metalcutting process, as the material for this type of screw must not be compressed, as is the case with thread rolling, for example. Titanium in particular, which is mainly used in the human body because of its good biocompatibility, tends to burn if the material is compressed too much.
As a machining process, thread whirling has been established for many years. Conventional thread whirling is a process that is mainly used on Swiss-type lathes to manufacture bone screws, but also on a larger scale for the production of threaded spindles.
In the process, the rapidly-rotating whirling head is positioned eccentrically to the workpiece axis in front of the guide bush of the sliding-headstock lathe and the slowly rotating workpiece is guided into the whirling head with an axial feed movement.
High Performance In Stainless Steels
Horn has developed a new, solid carbide milling cutter range especially for machining stainless steels. The tools are for milling stainless materials in the food, chemical and pharmaceutical industries as well as the precision engineering and watchmaking industries.
Due to their geometry and good chip breaking, the milling tools are suitable for machining numerous other materials. With the precise combination of the substrate, the macro and micro geometry as well as the IG3 coating, the milling system exhibits high performance and long tool life. The coating in particular offers high temperature resistance for machining steels alloyed with chromium, nickel and molybdenum.
Horn offers the solid carbide milling tools from stock in two types. The DSHPR variant is suitable as both a finishing and a roughing tool. The geometry is also adapted for trochoidal machining and plunging. The DSR type, with its very sharp cutting edge geometry and short design, is suitable for very small parts and unstable clamping conditions, such as in the medical and watchmaking industries. In the DSHPR line, all tools are available with four teeth and in diameters from 2 mm (0.079″) to 20 mm (0.787″). Horn offers the DSR variant with three teeth in diameters from 1 mm (0.039″) to 10 mm (0.394″).
Superfinishing Of Bores
Horn presented an innovative extension for the Supermini system in the field of ultra-fine machining. The precision tool manufacturer added a variant with a precision-ground rake face to the Supermini system especially for ultra-fine machining of bores.
Due to precision grinding of the cutting edge, it is free from notches when magnified approximately 200 times. The tool system can be used from an inside diameter of 0.3 mm (0.012″).
The sharp insert geometry enables process reliability even with very small infeed and cutting feed rates. The specially developed coating is suitable for stainless steels, non-ferrous metals and other metallic materials.
The insert of the Supermini Type 105 system requires only one tool holder for well over 1,000 insert variants. This applies equally to left-hand and right-hand versions. The carbide inserts are available in coated and uncoated versions in different grades for every application including hard machining up to 66 HRC. The patented droplet shape of the cross-section has a vibration-damping effect and delivers excellent repeatability when changing the insert.
Internal coolant supply to the insert increases tool life, enhances cutting performance and improves chip removal. Horn offers the tools with elements for face clamping. This allows, for example, the insert to be changed easily without having to remove the holder from the machine.
Related Stories:
Power Of Precision: ANCA Presents The Ultra Experience For Small Tool Perfection
YG-1 Unveils New Generation Captive Indexable Drill
High Accuracy And Absolute Repeatability For Medical Technology
Edmund Boland Appointed As GM Of ANCA CNC Machines
Ningbo Rail Transit Selects SKF Technology For Bearing Life Extension Project
Metal Cutting Helps Researchers Understand Metals’ Behaviour Under Extreme Conditions
ISCAR’s Shrink Upgrade: Empowering Precision with Advanced Tool Holding
Tesla Leverages Malaysia Tariff Liftings For A Later Grand Entrance
A*STAR Leads R&D Programme With 10 Industry Partners To Develop High-Performance EV Components
WANT MORE INSIDER NEWS? SUBSCRIBE TO OUR DIGITAL MAGAZINE NOW!
CONNECT WITH US: LinkedIn, Facebook, Twitter
Letter to the Editor
Do you have an opinion about this story? Do you have some thoughts you’d like to share with our readers? APMEN News would love to hear from you!
Email your letter to the Editorial Team at [email protected]